Manual operation, without hood, with optional heat exchanger
The F500 Basic is operated manually, open at the top (without hood) and can be optionally equipped with a heat exchanger to use the process heat. The throughput rates depend on how efficiently you integrate the manual interventions into your daily routine.
The fully automated version of the F500 Basic, which is equipped with a heat exchanger as standard, is the F500 Pro.
You can find a detailed comparison of all plant models here.
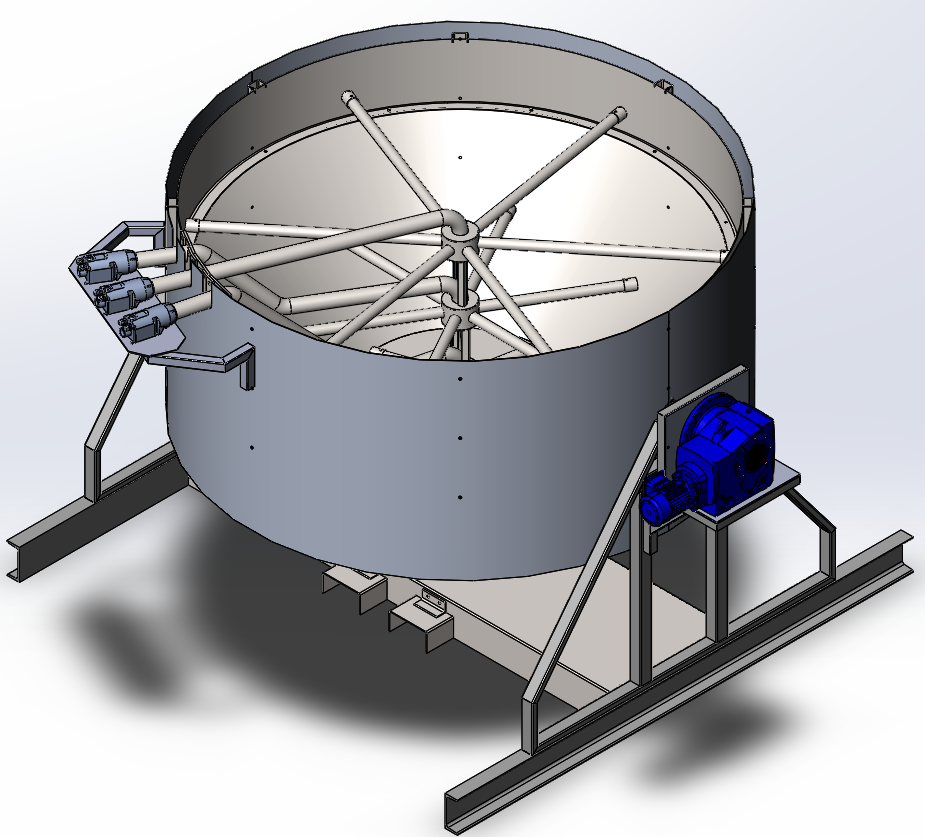
The F500 Basic can be optionally equipped with a heat exchanger.
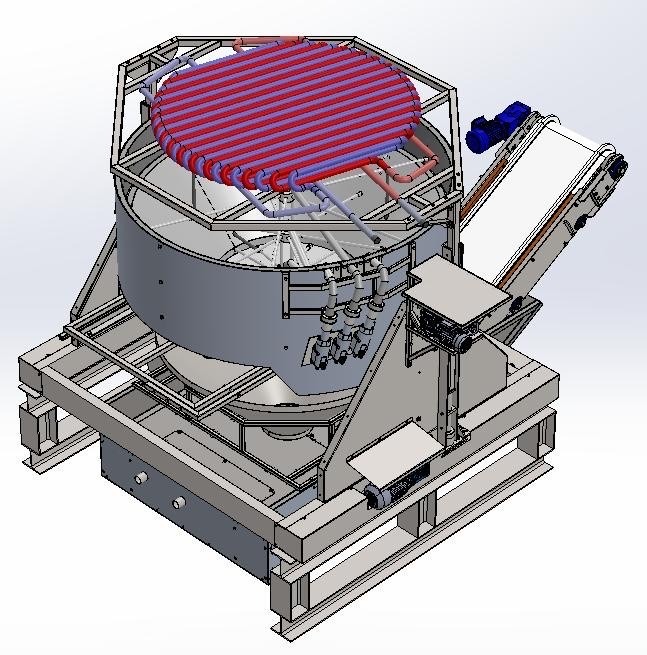
Control: Manual
The loading of raw material, ignition, monitoring of the pyrolysis process, emptying and quenching are all carried out manually with the F500 Basic. A control panel is provided to initiate the electrical ignition and to operate the motor for emptying the reactor.
Feeding the material directly into the reactor
The uncovered reactor can be filled directly. A front loader, for example, can be used for this purpose. The diameter of the reactor is dimensioned so that bucket sizes up to 2 m wide can be used.
Emptying the reactor and quenching
At the end of the pyrolysis process, the reactor is tilted using the mounted electric drive. A steel tray or sheet must be placed underneath the reactor to collect the biochar from the tilted reactor. The biochar is then quenched by hand with water.
Setting up the plant
The plant can be set up quickly and easily. Transporting and unloading it at the installation site is a simple operation.
Three-phase connection
The turbines are ignited and operated electrically. A rated current of 32 A is required.
Water connection
Water is needed to quench the biochar. Clean well water is sufficient.
Outdoor installation
The plant is installed outdoors. As the reactor is open at the top, it must be ensured that it is positioned far enough away from any combustible material.
Basic paved surface
A simply paved and level surface is required for the installation of the plant. Concrete is the most suitable surface. An area of approx. 16 m² (approx. 4x4 m) is required.
Key data
Throughput
The raw material throughput depends on various parameters:
- Bulk density of the raw material
- Daily operating time of the plant
- Structure / geometry of the raw material
When specifying throughput rates, it is important to distinguish between volume (m³) and mass (kg).
The reactor has a volume of 2.2 m³. Depending on the bulk density (kg/m³) and the water content or dry substance content, this corresponds to different masses.
Wood chips of size G35 have an average bulk density of approx. 220 kg/m³ with a water content of approx. 20%. Separated digestate from the biogas plant has a bulk density of approx. 650 kg/m³ with a water content of 70%. Accordingly, very different raw material throughput rates are obtained in terms of mass.
Raw material
In principle, many different raw materials are suitable as feedstock. These include wood chips, digestate, branch cuttings, shells, husks, stalks, tree bark.
The raw material with which the reactor is filled must have a maximum water content of 20%. You can use moister raw material, but then you have to dry it first. For pre-drying, you can use the waste heat from the Carbon Twister or other heat sources that may already be available to you, such as excess waste heat from a biogas plant.
Heat use
The reactor of the F500 Basic is open at the top. A heat exchanger is not installed as standard. However, it is available as an option.
Excess heat can be used as heating energy to heat buildings or stables, to pre-dry raw material, to dry grain or to feed into a district heating network.
The exploitable heat quantity depends strongly on the calorific value of the raw material. The main parameters are the type of raw material (wood, straw, etc.) and the residual water content. For this reason, no general statement can be made in this regard.
However, because of the plant's open design, the heat exchanger's efficiency is very low compared to that of the F500 Pro. When using wood chips, output values of around 15 kW can usually be achieved.
Energy requirement
The material is ignited electrically by hot air. During the pyrolysis process, electrical energy is required for various units (fans, motors).
Approx. 10 kWh of electrical energy is required per batch, which corresponds to an average output of approx. 3 kW.
The plant at a glance
The scope of delivery of the F500 Basic includes the reactor, the electric ignition, the turbines for controlling the air supply and the motor for tilting the reactor. The heat exchanger is available as an option.
Compare the different models of the Carbon Twister.