Fully automated, with heat exchanger, for high throughput
The F500 Pro operates fully automatically, is equipped with a heat exchanger to use the process heat and is optimised for high throughput.
It is the "big brother" of the F250 Pro and has a higher throughput in direct comparison. As a result, more process heat is available for heat use.
In contrast to the F500 Basic, it is fully automated, equipped with a heat exchanger, has a hood and includes all additional components such as a bunker and a bath. You can find a detailed comparison of the three variants here.
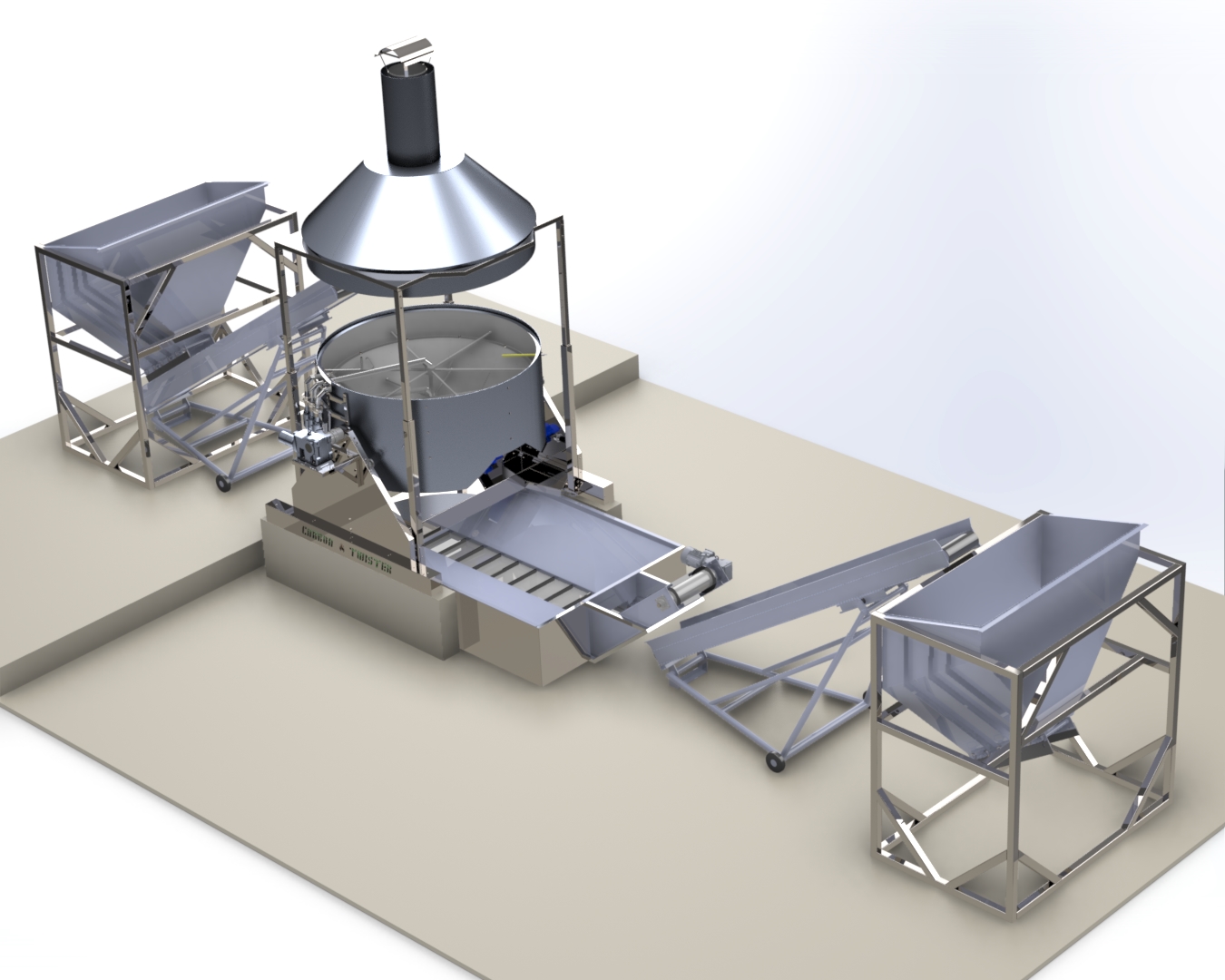
Control: Automatic or manual
Automatic control as standard
The F500 Pro operates fully automatically. The electronic control system performs the filling of the reactor with raw material, the pyrolysis process as well as the quenching and discharging of the finished biochar. You can monitor the progress of the process remotely.
All components such as turbines, pumps and motors are electrically operated.
Manual control possible
If you are running test series or would like to intervene manually in the pyrolysis process, you can do so at any time by deactivating the automatic control. This allows you to conveniently control each individual step of the pyrolysis process by hand.
Feeding the raw material
The raw material feed bunker holds exactly the volume required for a single pyrolysis pass. This bunker can be loaded in two different ways:
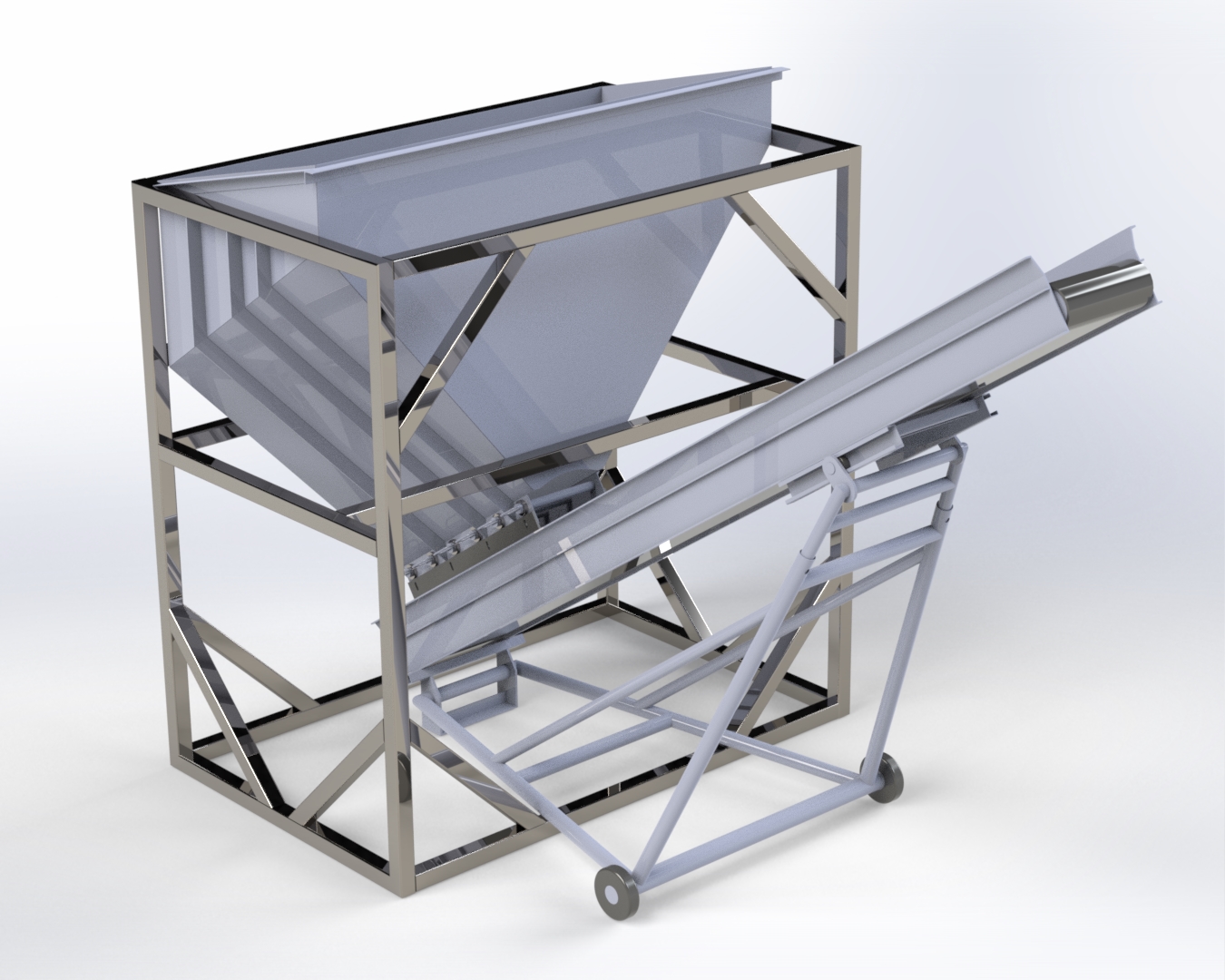
Loading by front loader
The filling opening of the bunker is approx. 2 m wide, making it suitable for standard front loader bucket sizes. You can fill the bunker, start the pyrolysis process and immediately reload the bunker for the next pass. In the following 5-6 hours, you can produce two batches of biochar fully automatically before you have to refill the bunker with the front loader.
Loading via feed hopper or silo
Instead of loading by front loader, an additional feed hopper or silo can be installed upstream of the bunker. Depending on its size, you can produce several batches without having to refill in between.
Setting up the plant
The plant can be set up and commissioned quickly and easily thanks to its modular design and outdoor installation.
Three-phase connection
The turbines, conveyor belts and pumps are ignited and operated electrically. A rated current of 32 A is required.
Water connection
Water is needed to fill the IBC container and as a backup for the integrated heat exchanger. Clean well water is sufficient. The pipe diameter must be at least 1 inch.
Outdoor installation
The plant is installed outdoors. An enclosure is not necessary.
Basic paved surface
A simply paved and level surface is required for the installation of the plant. Concrete is the most suitable surface. An area of approx. 60 m² (approx. 6x10 m) is required.
Key data
Throughput
The raw material throughput depends on various parameters:
- Bulk density of the raw material
- Daily operating time of the plant
- Structure / geometry of the raw material
When specifying throughput rates, it is important to distinguish between volume (m³) and mass (kg).
The reactor has a volume of 2.2 m³. Depending on the bulk density (kg/m³) and the water content or dry substance content, this corresponds to different masses.
Wood chips of size G35 have an average bulk density of approx. 220 kg/m³ with a water content of approx. 20%. Separated digestate from the biogas plant has a bulk density of approx. 650 kg/m³ with a water content of 70%. Accordingly, very different raw material throughput rates are obtained in terms of mass.
When operating at high capacity utilisation, the throughput will be between 1,000 and 3,000 tonnes or around 4,500 m³ per year, depending on the material, its bulk density and residual moisture.
Raw material
In principle, many different raw materials are suitable as feedstock. These include wood chips, digestate, branch cuttings, shells, husks, stalks, tree bark.
The raw material with which the reactor is filled must have a maximum water content of 20%. You can use moister raw material, but then you have to dry it first. For pre-drying, you can use the waste heat from the Carbon Twister or other heat sources that may already be available to you, such as excess waste heat from a biogas plant.
Heat use
A heat exchanger is integrated into the hood of the Carbon Twister. A frost-protected water-glycol mixture is used as the carrier medium. The pyrolysis process itself requires heat; however, with the exception of the ignition phase, it supplies this heat itself. The excess heat that is released can be recovered via the heat exchanger.
This heat can be used as heating energy to heat buildings or stables, to pre-dry raw material, to dry grain or to feed into a district heating network.
The exploitable heat quantity depends strongly on the calorific value of the raw material. The main parameters are the type of raw material (wood, straw, etc.) and the residual water content.
For this reason, no general statement can be made in this regard. In the case of wood chips, output values of around 200 kW can usually be achieved.
Energy requirement
The material is ignited electrically by hot air. During the pyrolysis process, electrical energy is required for various units (fans, motors, conveyor belts, pumps).
Approx. 10 kWh of electrical energy is required per batch, which corresponds to an average output of approx. 3 kW.
Depending on the material properties, 0.5 litres of bioethanol (spirit) may also be required per batch.
The plant at a glance
The most important key data of the F500 PRO at a glance.
Compare the different models of the Carbon Twister.
Compare with other plant variants
Plant modules
View a detailed description of the individual plant modules.