Batch process for maximum flexibility
In a batch process, the raw material to be pyrolyzed is fed in stages for each pass. One batch takes 2-3 hours to pyrolyze, depending on the nature of the raw material. Each batch consists of four basic steps, which always repeat themselves:
Filling the reactor with raw material.
Pyrolyzing the raw material in the reactor.
Removing the biochar from the reactor.
Quenching the biochar.
Manual filling and continuous material feed
Material feed in the batch process can be carried out in two different ways.
Either the system is operated in the daytime and new raw material is refilled after each batch. This is usually done using a front loader. Or you can opt for an upstream feed hopper or silo that holds enough material to fill the plant continuously, even without you being present.
Process flow and modules
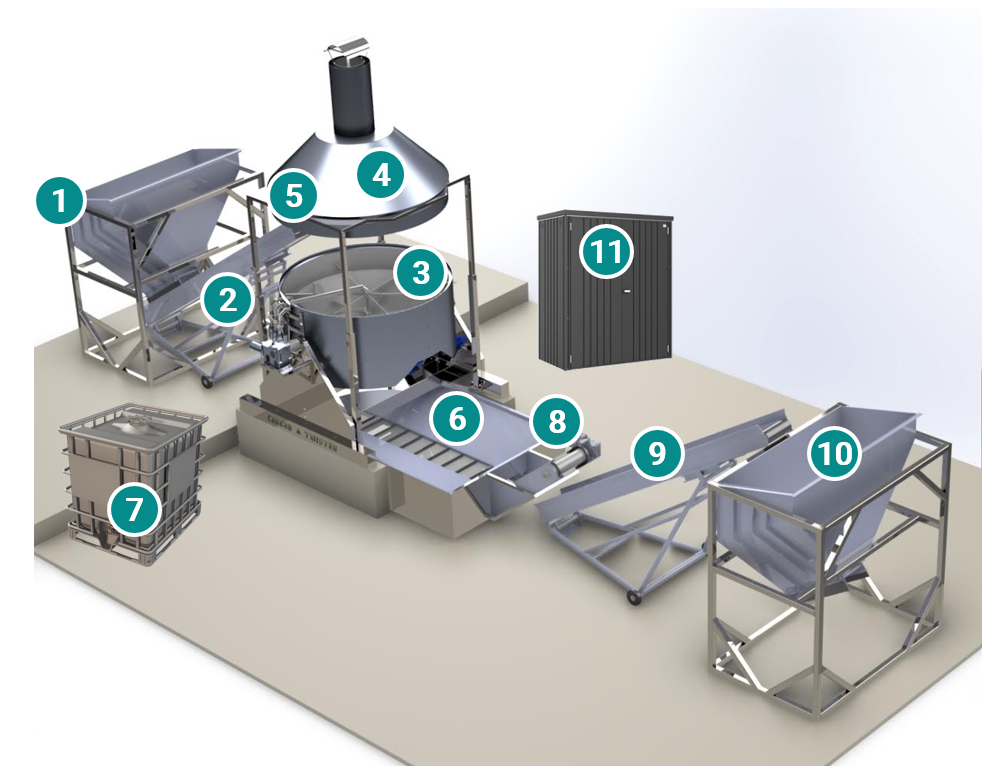
- Raw material bunker (Raw material)
- Conveyor belt
- Reactor
- Hood
- Heat exchanger
- Quench bath
- IBC container
- Conveyor belt in quench bath
- Conveyor belt to storage bunker
- Storage bunker (biochar)
- Equipment cabinet
1. (Raw material) bunker
The raw material to be pyrolyzed (input material) is fed in via the raw material bunker. The outlet features an opening that can be closed by a motor in order to regulate the feed to the downstream conveyor belt. The raw material bunker can be filled either using a front loader or by means of an alternative material feed (e.g. feed hopper with conveyor belt, silo) to be agreed upon on an individual basis, enabling automatic filling.
2. Conveyor belt for raw material
The conveyor belt is positioned at an angle to the vessel. It transports the material that falls out of the outlet opening of the raw material bunker into the vessel.
3. Reactor
In the reactor, the raw material is pyrolyzed into biochar. The reactor is made of heat-resistant boiler steel and clad on the outside with an aluminium shell. It incorporates an electrically operated system for igniting the material and various ducts for targeted control of the air supply to the interior. An opening that can be closed by a motor is located at the lower end of the vessel, through which the biochar leaves the vessel.
4. Hood
After the reactor has been filled, the electrically driven hood is lowered to seal the vessel. The hood encloses the integrated heat exchanger and discharges the resulting flue gas via a chimney. It is made of boiler steel, is thermally insulated and clad on the outside with an aluminium shell.
5. Heat exchanger
The hood contains a tubular heat exchanger which allows the process heat generated in the pyrolysis process to be utilised. The heat output depends on the raw material, the bulk density and the residual moisture. The transfer point for the carrier medium is at the lower end of the hood (2 pipes / flow & return).
6. Quench bath
The quench bath is located below the reactor. The bath is typically filled with water, but can also contain a nutrient solution. An IBC container pre-filled with liquid is used to fill the bath. The biochar is quenched when it falls into the water bath.
7. IBC container
The IBC container serves as a storage tank for the liquid (water or nutrient solution) needed for quenching the biochar in the bath. It is periodically refilled with fresh water via an electric valve control.
8. Conveyor belt in quench bath
An electrically operated conveyor belt is integrated in the quench bath. While the water or the nutrient solution is pumped back into the IBC container after quenching, the finished biochar is transported via the conveyor belt to the storage bunker.
9. Conveyor belt to storage bunker
The conveyor belt picks up the biochar from behind the quench bath and transports it, for example, to an optional storage bunker.
10. Storage bunker
The finished biochar can be stored temporarily in the storage bunker before it is processed further. It can be opened via a motor-driven flap at the lower end.
11. Equipment cabinet
The equipment cabinet contains electronic control components and other equipment required for operation.